「原形製作方法違いがGFRP成形体の寸法精度に与える影響」に関するpdf資料はこちら。
背景
FRP(Fiber Reinforced Plastics : 繊維強化プラスチック)の成形における出発点は、その実物モデルである原形型の製作である。原形型から形状転写する形で生産型を製作し、その生産型の成形面にマトリックス樹脂を含浸したガラス繊維を積層するという方法でFRP成形体は作られる。従来は形状再現技術の高い木型職人がこの役割を担っていたが、職人の高齢化や技術伝承の課題が生じている。これを踏まえ、代替の原形型製作手法の検討を行う必要があるが、異なる手法で製作された原形型から成形されるFRP成形体についての技術的な調査は前例も少なく、自社での評価経験もない。そこで同一形状のFRP成形体について、従来の木型職人による原形型製作に加え、機械加工(NC加工)、並びに3Dプリンティングによって原形型を製作し、原形型製作方法の違いがFRP成形体の形状精度に与える影響について調査することとした。
目的
機械加工、3Dプリンティング、木型職人による手作業でそれぞれ製作された原形型を用いて成形されたFRP成形体について、形状精度の比較評価を行う。
結論
木型職人による手作業のものと比較し、機械加工、3Dプリンティングの原形型で製作されたFRP成形体は、多くの形状項目においてより高い形状精度を示した。
概要
形状計測はノギスなどの接触式とレーザによる非接触式で行った。接触式で計測した代表的な寸法について、寸法計測結果の狙い値からの誤差をグラフにしたもの、並びに非接触式計測によるモデルと実測の形状誤差を照合計算したもの(図は機械加工の原形型による)をそれぞれ右下図に示す。狙い値からの誤差の比較から、機械加工と3Dプリンティングは、木型職人のものと同等以上の精度でFRP成形体を得られることを確認した。また、照合計算を確認したところ、3Dプリンティングでは冷却収縮に由来する形状ひずみが生じていた。幾何寸法については、機械加工で製作した原形型から得られたFRP成形体が評価中で最も高い精度を示した。
本技術評価のコンセプト
本技術評価においては、機械加工、3D Printing、木型職人による手作業という3つの異なる手法によって製作された原形型で製作されるFRP成形体の寸法精度の比較評価が趣旨である。下図に本評価のコンセプトを示す。
機械加工、3D Printing、木型職人による手作業について、以降、それぞれMachining、3D Printing、Hand Processingと表現する。
評価準備と評価方法
原形型のモデル作成
原形型は下図で示す形状にてモデル製作した。モデル製作ソフトにはFusion 360を用いた。形状にはR加工や球面等を取り入れることで、FRP成形体の形状測定時に3D曲面形状精度評価を行うと同時に、計測の基準面を直線で構築することで2D寸法測定作業を安定させる形状とした。生産型並びにFRP成形体製作時に必要と考えられた抜き勾配について、垂直面の寸法が20mm程度と小さいことから、当該勾配を採用せずモデル化した。また基準面であるDatum面は、最終的にFRP成形体では凹凸のある解放面が生じる底面ではなく、フランジ面の上面部とした。尚、モデリングは当社のR&Dセンターにて実施した。
原形型の製作
3D Printingで製作する際はstlデータを、Machiningについてはstlデータに加え図面を提供した。Hand Processingで製作する際は図面のみを提供した。
FRP成形体の製作
原形型に生産型用のFRP材を積層、硬化させたのち、脱型することで生産型を製作した。生産型の脱型を阻害する凹凸を低減するため原形型表面の研磨を実施した。同様に生産型についても、成形面については研磨を行った。原形型の転写形状である生産型の外観写真を左下図に示す。
この生産型にFRPを積層して硬化させ、脱型することでFRP成形体を製作した。積層している様子を右下図に示す。尚、使用しているFRP材料は強化繊維がガラスマット、マトリックス樹脂は不飽和ポリエステルである。
生産型、並びにFRP成形体の成形はすべて当社工場にて実施した。
FRP成形体の寸法と表面粗さ計測
幾何寸法を含む寸法計測は下図で示す①~⑯および⑳の領域、表面粗さ⑰~⑲の領域について行った。測定環境は22℃、50%RHで管理した。
2D寸法計測には、ノギス(CD67-S20PSミツトヨ)、ハイトゲージ(HD-60AXミツトヨ)、マイクロメータ(PMU300-25MBミツトヨ)、CRノギス(CR0508東栄工業)を使用した。また、3D寸法を含むFRP成形体の全体形状計測を、三次元形状測定機(Quantum E S 2.5m 7-Axis FARO)にて行った。表面粗さ測定にはSJ-310(ミツトヨ)を使用した。一例として、ハイトゲージでの高さ測定、三次元形状計測機によるブルーレーザを用いた非接触計測の様子を下図に示す。
計測はすべて当社のR&Dセンターにて実施した。
結果
原形型のモデル作成
モデリングは問題なく完了した。また、Machining、Hand Processing向けに図面を作成した。
原形型の製作
Machining、3D Printing、Hand Processingで作成した原形型の外観写真を下図に示す。どの原形型も外観上は大きな問題は無かったが、3D printingのものについては厚み方向に積層するという工程の特徴上、厚み方向に凹凸が見られた。
FRP成形体の製作
原形型の製作工程によらず、FRP成形体は問題なく製作できた。ただし脱型を可能にするため、すべての原形型について生産型成形前、並びに成形型そのものに対しても表面を研磨するという処理を行った。
FRP成形体の寸法と表面粗さ計測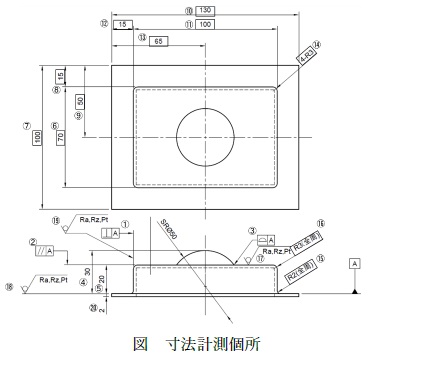
幾何寸法と2D寸法の計測結果を下表に示す。黒塗りで示した部分は、ノギスなどの接触式寸法計測機で計測が困難なもの、またはFRP成形体のトリミングラインに該当する部分で寸法計測が困難だった箇所を示している。右図には、評価準備と評価方法の章で示した計測番号①~⑯に対応する寸法を示した。幾何寸法は垂直度、平行度、輪郭度でそれぞれ0.1~0.4、0.3~0.9、0.8~1.8程度であり、Machiningで製作したFRP成形体が最も精度が高かった。高さや奥行きといった2D寸法については、原形型の製作方法によらず、狙い値からのずれが最大で1mm程度であり、同様にR寸法は0.8mm程度の差異を示した。特にR寸法においては、Hand Processingの狙い値からのずれが顕著であった。またレーザと接触式の両方で計測できた寸法について、レーザにて計測した方が計測結果は小さくなる傾向が明らかとなった。
以下、各形状測定結果の詳細を見ていく。
幾何寸法に関するグラフを右図に示す。幾何寸法は全体を通じてMachiningが最も優れていることがわかる。また垂直度や平行度と比較し、球体の輪郭度の精度が低い傾向は共通しており、特に3D printing、Hand Processingでは輪郭度が突出して高いということが明らかとなった。
高さや幅に関する2D寸法の比較をするため、狙い値からの誤差を縦軸としたグラフを下図に示す。ハイトゲージやノギスで計測した接触式である左下図と、レーザによる非接触式で計測した右下図で凡例が異なるのは、全高④がレーザによる非接触式は計測できなかったことによる。グラフ内には狙い値からのずれである誤差の数値をデータラベルとして記載した。Machiningと3D Printingが誤差の小さい傾向にある。既に述べた通り接触式と非接触式を比較すると、非接触式の方が計測結果数値自体は小さめになる傾向を示した。
角Rについて比較を目的として、狙い値からの誤差を縦軸として作成したグラフを下図に示す。接触式と非接触式で凡例数が異なるのは、凹部のRである角R⑮の計測が接触式ではできなかったことによる。比較結果から非接触式の方が計測値の低い傾向にあり、接触式では3D Printingが最も誤差が少なかった。
異なる製作方法で得られた各FRP成形体に対し、非接触式であるレーザ計測で取得したポリゴンデータと、原形型のモデルとの寸法誤差に関する照合計算によって得られたコンター図を下図に示す。尚、照合計算はモデルに記載したDatum面を基準面として行った。Machiningで製作した原形型から成形したFRP成形体は、最大で0.4mm程度フランジが底面側に反っている以外は、0.1~0.2mm程度大きめにできているものの、全体的にモデル形状に近い寸法でできていることがわかる。3D Printingについては、フランジ端面が上面側に反る傾向が見られ、またフランジの角部が最大で0.8mm程度小さめにできており、全体的にはMachiningと異なり若干小さめにできていた。同様にHand Processingについて、0.4mm程度フランジが底面側に反っていることに加え、垂直面が0.8mm以上大きめにできており、上面部は0.1mm程度であるが小さめにできていることが明らかとなった。さらに球面部は部分的にではあるが0.9mm程度大きめにできていることを示しており、コンターバンドの上限である0.8mm以上となる灰色で示される領域があることを確認した。
表面粗さの計測結果を右表に示す。水平面については原形型の製作方法によらず、全体を通じてRaで0.7μm以下であり、Ptでも最大5.2程度であることから、表面状態は全体的に良好であった。垂直面についても数値は概ね水平面と同等の数値範囲であったが、Machiningについては他と比較し値が大きくなる傾向となった。
右表で得られた数値を、計測個所ごとにグラフにしたものを下図に示す。どの表面粗さ計測値も良好であったが、垂直面に関する計測結果において、MachiningのRzとPtが極端に大きくなっていることから、長波長のうねりによる凹凸が存在していたことが示唆された。
縦軸を厚み計測結果、横軸を計測位置としたグラフを左下図に、厚み計測位置は右下図に示す。狙い厚みの2mmに対し、多くのデータが3~4mmの範囲に存在することが分かった。尚、この厚みの値は原形型の寸法精度の影響は無く、FRP成形体の積層精度に依存することを加筆しておく。
考察
従来法以外の原形型製作方法の選択について
Machining、3D Printing、Hand Processingの3つの異なる手法で製作された原形型から作られたFRP成形体について、その精度の違いを述べた上で、代替可能かの判断、並びに適切な原形型製作方法の選択について提言を行う。
結論から言うと、Machiningと3D PrintingがHand Processingよりも精度には優位性があると考えられ、従来法の代替としてMachining、3D Printingによる原形型製作手法適用は可能と判断する。また、大型のものはMachining、小型のものであれば3D Printingを原形型とすることが望ましいと考えられる。以下、詳細を述べる。
Machiningは全体を通じて他と比較し、高精度を実現できる原形型製作法であることが明らかとなった。ただし、後述する通り表面粗さに一部難があることは付け加えておく。3D Printingは2D寸法精度において比較的高い精度を実現した。ただしこれは3D Printingの原形型の素材が難接着材のPP(ポリプロピレン)であるため、生産型成形前の表面処理工程が簡略化できていることも影響していると考えられる。本点については後述する角R精度に関する記述内で、推測の裏付けを述べる。
全体形状を俯瞰した照合計算結果を見ると、3D Printingの場合は冷却収縮によるひずみが各所に見られ、形状が変形しやすいという課題も示している。フランジ部分の浮き上がりやそれに伴う角部の角度減少は、一旦溶融したPPが再冷却過程で収縮したことで生じた変形と考えられる。本来3D Printingの得意とする中空断面を形成すると、その外面が中空領域に対して沈み込む等の変形が想定されるため、リブによる内部補強をはじめとした断面剛性向上が不可欠になる。この変形は原形型が大型になるほど顕著になると想定され、また大型化により積層時間がかかる等のデメリットが優勢になると考えられる。よって、大型のFRP成形体を得たい場合、3D Printingが原形型製作方法として適した選択肢か否かについて、慎重な判断が求められる。その一方で、3D Printingは各断面を積層していくため、複雑な形状構築を得意とする。生産型やFRP成形体の脱型という、FRP成形体の製作に向けたハードルを越えるための表面仕上げと形状設計は不可欠であるが、Machiningではできない形状を実現するには新たなツールになり得ると考えられる。
以上の議論を踏まえると以下のようになる。
FRP成形体で実現できる寸法精度について
最初に2D寸法について考える。Machining、3D Printing、Hand Processingで製作されたどの原形型を用いたとしても、寸法精度はFRP成形体実測として最大±1mm程度であることが明らかとなった。これは、寸法あたりに直すと約1.5%である。つまり、FRP成形体の公差設定は狙い値の1.5%程度を一つの指標として考えることが妥当であるといえる。
この1.5%はHand Processingの場合の公差設定であるが、3D Printingでもほぼ同等の1%、Machiningで0.6%と小さくなるものの、n数が少なく工程のばらつきへの考慮が必要である。工程によるばらつきが、仮に今回の狙い値からの誤差の50%と考えられると、Machining、3D Printing、Hand Processingについてそれぞれ狙い値の、0.9%、1.5%、2.25%を公差として設定するのが妥当であると考える。
角Rについては、3D Printingが接触式の結果において高い精度を示した。これは原形型の素材がPPという難接着材料であるオレフィンであるため、表面処理がMachiningやHand Processingのそれよりも工程が少ないため、追加工による寸法変動が起こりにくかった、ということが影響していると考えられる。ただし、非接触式の場合は狙い値に対して最大10%程度の誤差を示していることから、この程度の公差は必要と考えられる。Machiningは狙い値について最大11%程度の誤差を示し、Hand Processingは最大26%という大きな誤差を示した。これらについて同様に工程のばらつきとして50%分を考慮すると、Machining、3D Printing、Hand Processingについてそれぞれ狙い値の、16.5%、15%、39%を公差として設定するのが妥当であると考える。
幾何寸法については原形型の製作方法により大きな差が出た。Machiningの場合、垂直度や平行度など、平面や直線を基本とした幾何寸法で最大0.3mm程度を実現している。その一方で、この幾何寸法に対し3D Printing、Hand Processingはともに0.7~0.9mm程度の値を示していることから、幾何公差設定に1mm程度は必要と考えられるなど、精度は劣る。工程のばらつきを踏まえると、垂直度や平行度の設定はMachining、3D Printing、Hand Processingについてそれぞれ、0.46mm、1.36mm、1.02mmとなる。
曲面を含む複雑三次元形状の形状精度である輪郭度は、さらに厳しい結果となっている。最も高精度の結果の出たMachiningでも0.8mm程度、3D PrintingやHand Processingでは1.8mm程度と狙い形状に対して大幅なずれが確認された。この主原因は非接触式測定における照合計算の所でも述べたDatum面のひずみが影響していると考えらる。基準面が歪むと、照合計算における形状モデルの合わせ込みの際に実測データとの形状誤差が発生しやすく、幾何寸法精度は低下する。よって幾何寸法を優先とする場合、原形型はMachiningで準備することが妥当であることが、結果として示されたと考えるべきである。同様に工程のばらつきを踏まえると、輪郭度の設定はMachining、3D Printing、Hand Processingについてそれぞれ、1.18mm、2.65mm、2.7mmが一案であると考える。
表面粗さについては、原形型の製作法による影響もさることながら、生産型成形時の表面処理の影響を大きく受けていると考える。結果として表面粗さはRaすべてにおいて3.2μm以下であり、並仕上げの基準といえる3.2μmは実現できていると考えられる。ただし、表面処理方法の状態によってはRzやPtで7~9μmという値を示したことには留意が必要といえる。Machiningだけが顕著に表面粗さが低下するとは考えにくく、生産型、もしくはFRP成形体製作時における工程のばらつきにより、長波長を基本とした緩やかな凹凸が生じることが不可避であると考えられるためである。そのため、並み仕上げに該当するRzは12.5μmが妥当である。Ptは評価長さ区間での粗さ評価になるためRzよりも厳しいが、まずバックデータの少ない現状で設定するのであればRzと同等の値とすることに大きな問題は無いと考えられる。
厚みについては、原形型の影響はほとんどないが、FRP成形体に対する公差指標取得という観点で述べる。今回得られた結果により、厚み精度は概ねレンジとして3mm程度、公差として±1.5mm程度は必要である、ということが明らかとなった。ガラスマットはそれ自体が厚みを持っているため、成形体の厚み設定を考える際の一助とすべきである。
以上の結果を踏まえ、各代表的な形状寸法について、原形型の違いによって実現できる公差設定の一例を以下の通りまとめる。
接触式と非接触式で得られた形状計測結果の違いについて
同じ寸法計測個所である2D寸法を一例として、ノギスなどの接触式とレーザによる非接触式での結果の違いを考察する。両者の狙い値からの誤差をグラフ化したものを下図に示す。左下図が接触式、右下図が非接触式である。数値自体がばらついているが、一つだけ言える傾向が「非接触式で得られたデータの方が数値小さい」ということである。一例として、Hand Processing 幅⑥について、接触式では+0.95mm、非接触式では+0.337mmを示しており、数値として0.6以上小さい。
この背景にある事象について考える。ある板厚を有する平板の厚み(または幅)を計測する概略図例を右図に示す。モデル上は長方形だが、実際には凹凸がある。接触式で計測しようとする場合、右図中の赤のように、表裏(または左右)の凸部にて計測されると考えられる。一方で非接触式の場合、モデルとの形状の誤差、すなわち右図中でモデルよりも凸部である黒矢印や当該モデルより凹部となっている青矢印の誤差を計測し、その平均値から結果を算出すると考えられる。平面が極めて平滑な被検査体であれば接触と非接触はほとんど変わらないが、FRP成形においては、既述の通り手作業による表面仕上げが入るため、FRP成形体表面での凹凸の出現は避けられない。この場合、接触式で寸法を計測した場合と比較し、非接触式では凹部が考慮されるため、計測結果は小さな値になる傾向を示すと考えられる。
まとめ
Machining、3D Printing、Hand Processingという異なる手法で製作された原形型を用いて成形されたFRP成形体について、2D並びに3D形状寸法の精度を比較した。結果、Hand Processingと比較し、Machining、3D Printingともに同等以上の形状精度を実現していることを、定量的な検査結果データで示すことに成功した。これにより、従来のHand Processingに加え、Machiningや3D Printingが原形型製作に関する代替手法になることを示すことができた。
また得られた結果を踏まえ、異なる原形型で成形されたFRP成形体について、どのような寸法公差を想定すべきかについて提言を行った。合わせてHand Processingによる加工精度は、手作業であることを前提とすると高いレベルにあることも確認された。従来手法であってもある程度の形状精度を実現していたという事実を確認できた意義は大きいと考えられる。
今回得られた結果は、原形型製作工程に新たな選択肢、並びに考慮すべき公差設定の指標を示すことができたという意味で、当社にとって技術的に大きな前進である。
以上