「ASTM D5379によるガラスマット強化GFRPの面内せん断特性評価」に関するpdf資料はこちら。
背景
FRP(Fiber Reinforced Plastics : 繊維強化プラスチック)は強化繊維とマトリックス樹脂から構成される複合材料である。一次構造材に用いるFRPの強化繊維は、異方性の顕著なガラスロービングやカーボンストランドなどの連続繊維材料が適用される。しかしながら、FRPで一般汎用材料として用いられるのは、既定の繊維長にて切断後、ランダムに配向されたガラスチョップ繊維からなるガラスマットを強化繊維にしたFRPである。当該材料の構造部材への適用が進んでいることから、シミュレーションニーズも高まっている一方、これらの計算に必要な材料特性を評価した事例は少ない。シミュレーションの一つである応力解析には引張や圧縮だけでなく、異方性を考慮したせん断モードでの弾性率やポアソン比といった物理特性を把握することが不可欠であるが、現段階ではこれらのデータを取得できていない。この状況を踏まえ、ガラスマットと不飽和ポリエステルをそれぞれ強化繊維、マトリックス樹脂としたGFRPについて面内せん断特性を取得する。
目的
ASTM D5379に基づきDouble V-notch型試験片を用いたGFRPの面内せん断試験を行い、強度、0.2%オフセット強度、弾性率、破断ひずみ、ポアソン比のデータを取得する。
結論
強度、0.2%オフセット強度、弾性率、破断ひずみ、ポアソン比は平均値で、それぞれ92.8MPa、65.9MPa、3.17GPa、3.99%、0.46であった。
概要
試験片はガラスマットを強化繊維、不飽和ポリエステルをマトリックス樹脂としたGFRPを用い、 試験は23±3℃、Dryの環境にてn=5で行った。取得されたSS線図と試験の状況を下図に示す。SS線図からはひずみ1~1.5%を超えると非線形を示すことが明らかとなった。また、試験後の試験片はすべて右上から左下にかけて破壊が生じており、破壊モード判定から本試験が面内せん断試験として成功していることを確認した。
評価準備と評価方法
試験片用FRP平板製作
すべて同一の不飽和ポリエステル樹脂とガラス繊維を用い、3.5mm厚みを狙って縦300mm、横200mmの寸法でハンドレイアップにて1枚製作した。当該平板の図面を下図に示す。
面内せん断試験片加工
面内せん断用試験片の形状図面を下図に示す。本試験片形状はASTM D53791)に準拠したものである。
試験片の大まかな切り出し位置を罫線にて定義の上、複合材料裁断機(AC-500CF)を用いて矩形での切り出しを行った(左下図)。切り出した矩形体は、マトリックス樹脂の硬化収縮による面変形が生じていたため、平面研削盤(UPZ525NC II)にて面加工を行った。その後、プロファイル研削盤(UPZ210Li II)を用いて試験片中央部にノッチ加工を行った(右下図)。加工した試験片数は5本であり、試験片名称はVNS-1~5とした。
加工後の試験片は上図の図面に基づき全数検査した。
面内せん断試験
ASTM D53791)に準拠して実施した。試験数、環境、試験条件、取得データ、計測条件に関する概要を下表に示す。面内せん断強度、0.2%オフセット面内せん断強度、面内せん断弾性率、せん断ひずみ、ポアソン比はn=5の平均値を算出した。
試験片は二軸ゲージ(東京測器)をCN(ひずみゲージ用瞬間接着剤)にて貼付した。また試験結果の妥当性を確認するため、5本の試験片のうち1本については表裏両面に二軸ゲージを貼り付け、ASTM D53791)のSection 6.4 にあるねじり変形有無の評価を実施した。ねじり変形については、ひずみ0.004(4000με)における表裏の面内せん断弾性率( Gf、Gb )が下式を満たす場合に無視できると判断した。
試験設備に関する概要情報、並びに試験の様子を以下に示す。試験終了後、試験片の写真撮影を行った。
試験片の破壊状況はASTM1)中に示された表に基づいて判断を行った。
ポアソン比はASTM D5379では算出に関する記述が存在しないため、下式にて算出することとした。
上式中のひずみは下図のように定義した。
結果
試験片用FRP平板製作
平板を目視確認した結果、直径10mm程度のボイドがあった。試験片切り出し加工時は本ボイドを回避の上、加工を行った。
寸法検査結果の概要を述べる。縦横寸法について、それぞれ303mm、203mmであり、公差上限よりも2mm大きくなっていることを確認した。板厚はマイクロメーターで計測し、3.303~4.331mmとなり公差上限よりも最大で0.8mm程度厚めになった。またダイヤルゲージで計測した結果、平板の平面度は1.715mmであり図面要求を満たせなかった。平面度が大きくずれたことから定盤の上にFRP平板を置き、平板端面の「浮き量」をシックネスゲージで確認したところ(右図参照)、最大で1.8mmの浮きを確認した。
面内せん断試験片加工
加工後の試験片の外観写真を右図に示す。加工後に端面の損傷や層間剝離は認められなかった。
面内せん断試験片の寸法検査結果一覧(一部外観検査結果含む)を下表に示す。すべての寸法について図面要求を満たしていた。
面内せん断試験
n=5の平均値である面内せん断試験結果を下表に示す。
試験後の試験片の外観写真を下図に示す。すべての試験片について、右上から左下に破壊領域が分布している様子を確認した。本破壊モードは、ASTM D53791)でランダムに繊維の配向したSMC材の適切な当該モードとして定義された「AGN」に該当した。
ねじり有無を確認するため、表裏のひずみから算出した面内せん断弾性率の誤差割合を算出した結果、0.7%となり3%よりも低いことから、ねじりモードの変形は本試験中に生じていないことが明らかとなった。
また代表的なSS線図を下図に示す。図中、青線で示しているのは近似直線であり、X軸右側にシフトしているのが0.2%オフセット面内せん断強度を算出するための近似線である。どの試験片についても、およそひずみ1%超から非線形を示していることが明らかとなった。また試験片のうち数本は、歪み2.2%から3.2%という最大応力を示す前段階で初期破壊に由来する線図の変形を確認した。
考察
ポアソン比の値について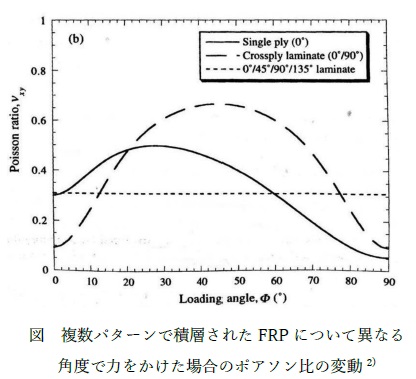
疑似等方に積層された連続繊維を強化繊維としたFRPではポアソン比は0.3程度、0°と90°のみに連続繊維が配向した直交積層や、特定の方向(0°)のみに連続繊維が配向したものでは、力のかかる方向によって当該値はそれぞれ0.05~0.5、0.1~0.7程度を示すことがわかっている2)。この関係を縦軸に面内のポアソン比、横軸に力をかける角度を相関図として示したものを右図に示す。
今回評価したGFRPは不飽和ポリエステルをマトリックス樹脂として、強化繊維には規定長さにカットされたガラス繊維をランダムに配向したガラスマットを強化繊維としている。ランダム配向であるため、疑似等方と同等の0.3程度を示すと想定されたが、今回はそれよりも大きな値となった。本相違点の主因について考察する。
既述したポアソン比の評価2)では、矩形の試験片を引張ることによって求めているため、応力集中が殆ど存在しない理想的な状況での評価になっていると考えられる。その一方で今回評価したGFRPは強化繊維がランダムに配向していることから矩形体での面内せん断特性評価が不可能であるため、double V-notchという形状タイプの試験片を用いている。本試験片形状ではV-notchをつけることにより応力集中を回避し、評価範囲においてできる限り均一に応力が分布するよう設計されている。過去にはノッチ先端のR、ノッチ間の距離、ノッチ角度等が検証されていた3)。ノッチ間距離の最適化検討の一例を右図に示す(評価対象は連続繊維を疑似等方積層したもの:[0/+45/-45/90]2s)。本検討においては、右図中0.2、及び0.225NDRが評価領域における応力分布が一定であるという判断がされている。
面内せん断応力分布図を見るとわかるように、+45°方向と-45°方向でそれぞれ引張、圧縮という異なる荷重モードが生じていることがわかる(本図中はASTM D5379とは違い、ノッチの右側を上に引張り上げるという荷重を想定していることに注意)。これらの事前情報を踏まえ、今回得られたポアソン比について考察する。
一つの可能性が、材料そのものの有する異方性によるものである。今回評価したGFRPでは、一般的には均質材と想定されている。しかしながら、引張弾性率と比較して圧縮弾性率が低いと想定すると、同じ荷重が引張と圧縮でかかった場合、異方性の無い均質材と比較し、圧縮ひずみが引張よりも大きくなる。これはポアソン比の上昇となり、均質材で0.3程度と予想された当該値の増加の可能性の一つとなる。試験後の試験片をみると、実際に圧縮方向での破壊(右上から左下へ破壊)が進行していることから圧縮破壊が優先的に進行しており、本推測を支持する一事象と考えられる。本事象の裏付けは圧縮試験を行うことで圧縮弾性率を取得し、引張弾性率と比較するというのが一案である。
もう一つの可能性として、試験片に貼り付けたゲージ角度の誤差という可能性が考えられる。ゲージの角度がずれることで評価領域の圧縮と引張という応力分布状況に変化が生じ、例えば引張領域を計測するひずみゲージがより圧縮領域に、同様に逆のことがもう一つのひずみゲージに生じることでポアソン比が等方材料よりも大きくなったというものである。本仮説の妥当性は詳細な応力解析によって検証していきたい。
不飽和ポリエステルを用いたGFRP圧縮系試験における形状精度実現の重要性
試験片を用いた材料試験では試験片の形状精度がポイントである。引張試験と比較し、圧縮試験では特に試験片形状の精度が大変重要となる。これは、圧縮系試験では試験片の精度が低いと、試験中に試験荷重が軸心からずれる偏荷重が生じ、試験データの正確性が低下することに加え、試験治具や試験機に試験荷重が伝わることで当該治具や試験機が破損する恐れがあることに由来する。
評価したFRPのマトリックス樹脂として用いた不飽和ポリエステルは、硬化時に体積が低下する硬化収縮が大きい。この影響から試験片加工用FRP平板は、平面度が1.7mmを超え、定盤に置いた際に最大1.8mmの浮きが生じるなど、FRP平板成形精度に課題があった。プレス機による成形でこの成形精度は改善できる可能性もあるが、今回評価したいのは「ハンドレイアップで成形したGFRP」であるため、プレス機等のハンドレイアップとは異なる均一荷重はかけられない。ハンドレイアップ成形では一般的には片面は成形面にできる一方、裏面は強化繊維由来の凹凸のある解放面であるのが一般的である。そのため、両面を成形面とするには成形時にFRP平板を一度裏返す必要があるなど、高精度のGFRP平板の成形は困難であった。このような背景もあり、成形後のFRP平板は試験片寸法に近い矩形に切り出した後、成形面を追加工することにより今回適用した面内せん断試験に使用できる形状精度を実現した。 上述の加工工程の見直しによる試験片形状精度実現により、結果でも述べた通り試験中にねじりが生じていないことを確認できていることから、今回得られた面内せん断試験データは妥当であると考えられる。
面内せん断特性におけるSS線図の解釈について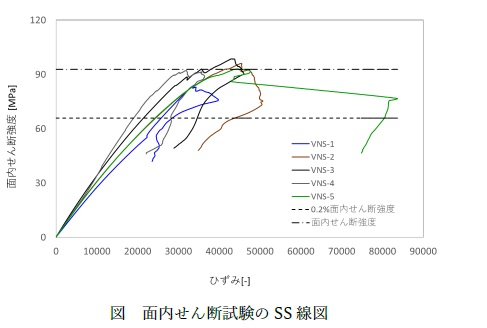
面内せん断試験によって得られたSS線図(ひずみ-応力線図)を右下図に示す。各試験片の当該線図を色分けして示し、0.2%オフセット面内せん断強度、面内せん断強度の平均値を破線として示している。
各試験片のSS線図を拡大して検証した結果、ひずみが概ね1.0~1.5%を超えたあたりから非線形領域が出現する傾向にあった。これに対し、ヒステリシスを示さないとされる0.2%オフセット面内せん断強度を示したひずみは2~2.5%であり、上記のひずみより1%程度大きな値となっている。LCF(Low Cycle Fatigue)のような実使用上で日に数回程度の荷重負荷であれば、0.2%オフセット荷重とその際のひずみを設計許容値として用いるのは大きな問題は無いと考えられる。しかし、1分間に数回から数十回の負荷というようなHCF(High Cycle Fatigue)を想定するのであれば、SS線図上で非線形が生じない歪み1.0~1.5%程度を負荷上限として想定すべきと考えられる。いずれにしても、FRPはヒステリシスを示さないのはもちろん、弾性域で使用するのが一般的であり、かつ長期寿命の評価には繰り返し疲労負荷に対する応答挙動評価が重要である。よって、今回得られた材料データだけで設計許容値を判断するのではなく、複数水準の応力比による動的疲労試験を実施することは不可欠であると考えられる。
また、VNS-5が高ひずみ領域で示した線図の挙動を考察する。右上図で見てもわかるように、VNS-5のみが50000μst以上の領域でひずみ軸にほぼ平行に線図が推移する、すなわち応力が増加せずに変形だけが進行するという状況がみられる。本状況を検証するため、せん断ひずみ( ε1+ε2)が50000μstを超えた領域でのε1 とε2 の関係をグラフとして示したのが右図である。尚、ε1 とε2 については本報の5頁の式を参照のこと。右図中では時間経過に伴い、 ε1の軸に対し、右側から左側にひずみデータが移動する(右図中の矢印の方向)。これは、試験の進行に伴い、引張に該当するひずみが緩和され、圧縮ひずみは維持されることを意味している。本事象を説明するにはASTM D5379という材料試験自体の特徴を理解する必要がある。
ASTM D5379は高ひずみ領域で強いひずみ分布を示すことが知られている。Matthewらはこのひずみ分布の状況をDIC(Digital Image Correlation)によって明らかにした画像を紹介している。当該評価結果を右図に示す3)。評価した材料は異方性の無いPU(ポリウレタン)樹脂である。右図を見ると、せん断ひずみは試験変位増加に伴い右上から左下にかけて圧縮による高いせん断ひずみ分布を示していることがわかる。このような特徴的なせん断ひずみ分布が前頁で示したような圧縮ひずみが優先的に高まるという事象につながっていると判断する。
以上の通り、ある程度以上のせん断ひずみがかかると、せん断試験で回避すべきひずみ分布が顕著になり、試験としては不適切になっていると考えるべきである。よってASTM D5379においては、高ひずみ領域の評価データをせん断荷重モードのデータとして扱うのは不適切であり、およそ50000μst以上のせん断ひずみの生じる領域でのデータの解釈には注意が必要である。
まとめ
ガラスマットを強化繊維、不飽和ポリエステルをマトリックス樹脂としてハンドレイアップで成形したGFRPについて、面内せん断試験を実施し、面内せん断特性として強度、弾性率、ポアソン比、0.2%オフセット強度のデータ取得に成功した。今回得られた結果から、当該GFRPは面内せん断モードの荷重負荷に対して異方性を示している可能性が高く、応力解析等のシミュレーションには今回取得したデータを用いることが必要であると考えられる。歴史の長いガラス繊維マットを強化繊維としたGFRPのせん断特性評価として大きな一歩であり、今後、当該試験手法を用いてGFRPの層間せん断特性の取得を進めていく。
参照文献
1) ASTM D5379/D5379M-12, Standard Test Method for Shear Properties of Composite Materials by the V-Notched Beam Method.
2) Hull, D., Clyne, T. W. (1996). An Introduction to Composite Materials (2nd Editioned.). Cambridge: Press Syndicate of the University of Cambridge.
3) Matthew Crossan, Jeffrey T. Wood, (1996). Mechanical Characterization and Shear Test Comparison for Continuous-Fiber Polymer Composites. The University of Western Ontario.
以上